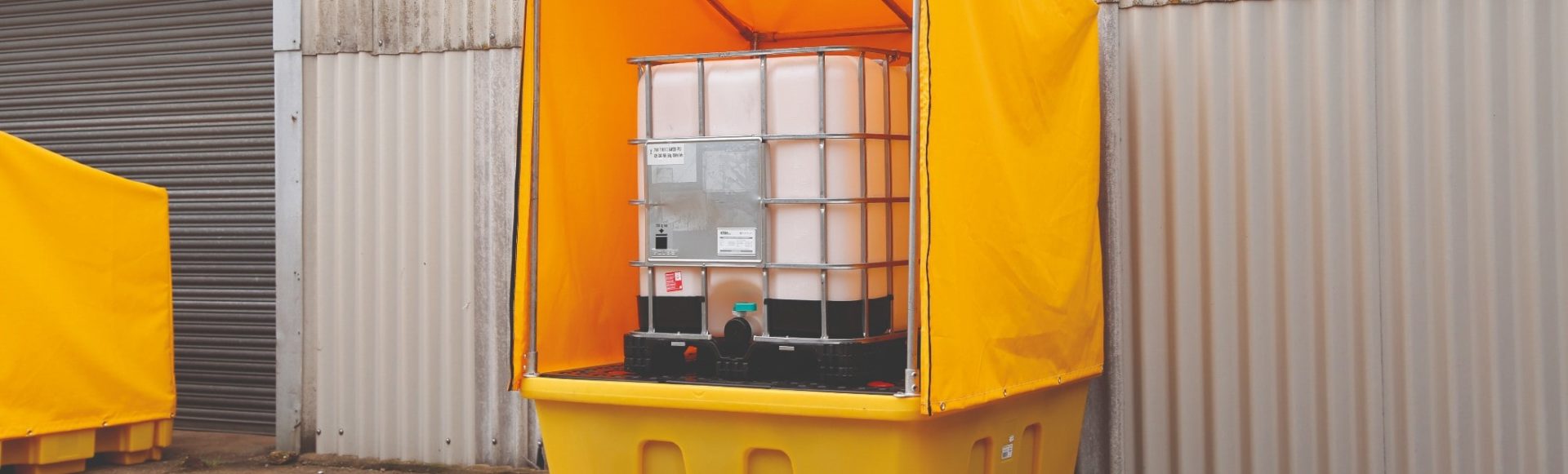
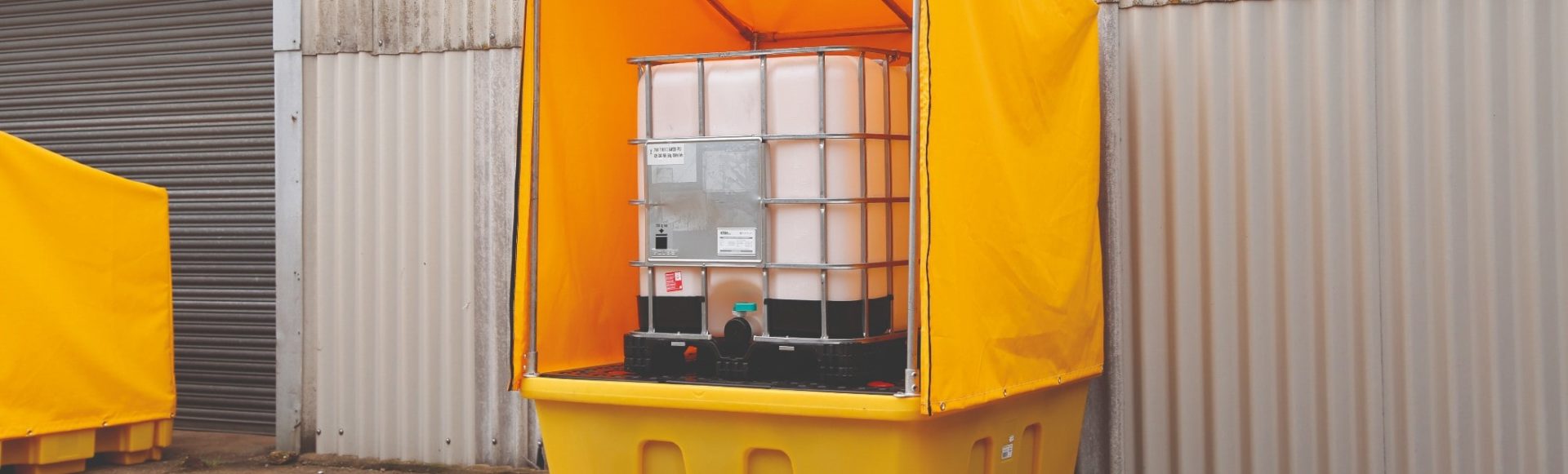
Drum Or IBC Storage: What Are The Key Advantages?
When it comes to storing large quantities of industrial liquids such as chemicals and oils, your choice of vessel depends on the volume and characteristics of the liquid that needs to be contained. To ensure safe storage and transportation of large volumes of liquids, businesses and organisations in the U.K. most frequently use storage vessels such as IBC tanks and chemical drums. The first factor that should be considered when choosing between a drum or IBC is adhering to health and safety regulations laid out by law.
When considering how to store large volumes of non-hazardous chemicals, the steel or plastic drum has been widely accepted as the best way for liquid transportation and bulk storage for businesses. Non-hazardous chemicals, fuels and hazardous goods have been transported around the world for decades by using these drums. However, over the last few decades, IBC storage tanks have had key advantages over their cylinder-shaped counterparts. In some cases, IBC’s can save businesses up to 75% by switching from drums and they can be moved freely and without expensive pallets and shrink wrap.
There are pros and cons to using both drums and IBC’s, it all comes down to the quantities and transportation of the liquids you are looking to store. Getting the best ROI while transporting your product depends on factors such as the cost of manufacturing, the cost of packing, transport, and even storage viability.
The right containers can save your company money at nearly every stage. If you are struggling to decide precisely which of these storage solutions are best suited to your needs, read on to discover the key benefits and features of drums or IBC storage containers.
What is a storage Drum?
Storage drums are a very common transport container for many hazardous and non-hazardous goods. Typically made of either metal or plastic, drums have long been a stand-by for a variety of industries. Until innovation started making headway in other options, they weren’t a bad choice, as they were stable, strong, and predictable in size and weight.
The number of storage drums held by a given container can range from less than 10 to well over 100 and are considered to be a form of secondary containment. Their cylindrical shape is both sturdy and space-efficient for storing and transporting, and as a result, the use of storage drum containers is very common at worksites that need to contain or distribute liquid substances in bulk.
Due to the significant association with hazardous materials or liquids of large quantities, drum storage containers are subject to a variety of quality standards related to the safe storage of drums. Some examples where these regulations will be paramount are the safe use of the plastic drums that house corrosive materials as these could require different safety procedures compared to those needed for the handling of metal drums housing explosive materials.
If the material held by the drum is flammable, the storage unit will be subject to additional legal and consensus standards, such as the HSE Explosive Atmospheres Regulations 2002 (DSEAR).
One of the issues surrounding round drums is that it’s very difficult to get all of a liquid or viscous product removed from a drum, even with a gravity-assist dispenser. That leads to increased product waste and reduced ROI. Finally, drums typically need to be thoroughly cleaned for sanitary or safety reasons which can lead to paying for more staff, cleaning materials, and time to do so between fillings and deliveries.
What is an IBC?
Intermediate bulk containers (IBC) and drums are the ideal solutions for shipping liquids in mid-sized volumes. They are usually made with a galvanised steel outer frame and an inner container of high-density polyethylene. IBC tanks are stackable and are typically mounted on a pallet for easy transportation using a forklift or a pallet jack.
The nature of the chemicals that can be stored in a given IBC tank depends on its packaging symbol. Depending on their classification, they can be used for the storage of hazardous materials such as corrosive chemicals. UN-certified IBCs can be used for storing and transporting hazardous materials, whereas non-UN IBCs are for non-hazardous bulk storage.
IBC containers with liners are arguably the best choice for shipping, storage, and dispensing large volumes of liquids. These containers are a popular solution for industrial applications where having clean storage and transport is vital. With additional features such as liners, these tanks can be used multiple times, while drums are generally single-use-only
IBC totes eliminate product waste by draining completely, while drums collect the residual product, and they can even be recycled once their use has expired. Recycling an IBC is easy and is a service offered by a myriad of companies around the globe. If you’re using a bag-based IBC instead of those with plastic containers or bottles it’s even simpler, the bag is easily removed and recycled after use.
One of the main benefits of an IBC is how easy it is to empty in comparison to a drum. When empty, it still takes a lot of manpower and space to move and store steel drums. An empty non-rigid IBC on the other hand can be folded down when not in use, allowing them to be stacked 10 high in storage and 5 high in most large logistics vehicles. Often special equipment is required to open and discharge both metal and plastic drums, which can introduce contaminants to the drum’s contents.
While IBC solutions are lightweight and effective, they can cost more than the average drum storage. Rigid bottle-and-cage IBC totes came along, eliminating that null space problem between rows of containers, but introducing new costs for manufacturers and buyers. The need to manufacture them with two different materials meant that the cost-per climbed upwards, negating many of the financial gains that changing shape offered.
Conclusion
Selecting the right container option for your company will translate to cost savings during your manufacturing and shipping process. In addition, investing in the right containers will result in fewer wasted product contamination problems caused by large spills. Always consider where you are storing your liquids, either inside a building or outside on site.
If you’re working with liquid and viscous substances, it is important to ensure that you’re getting everything you can from every intermediate bulk container or storage drum, regardless of contents or size. While switching to a new type of container may seem challenging in your current workflow, the effort is well worth it and will help improve your process from fill to sale and throughout the supply chain.
Spillshop offers over 160 different types of spill kits and storage solutions ranging from 15L to 1100L capacities. For further information on chemical safety and storage best practices, read our blog. If you have any questions regarding our solutions or securing best practice chemical storage in the workplace, contact our expert team today.